Industrial IoT for predictive maintenance
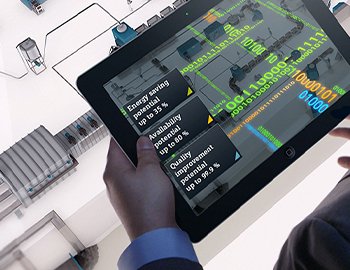
Industrial IoT for Condition Monitoring
Condition monitoring is a key element of PREDICTIVE MAINTENANCE(PM) that deals with detecting any unusual or unplanned breakdowns of machinery/equipment and evaluating the repair or replacement cost. Some of the main benefits of condition monitoring include:
- Better system-related reliability
- Better efficiency
- The decreased total cost of operation
- Reduced maintenance cost
- Prevention of unplanned maintenance
- Preventive maintenance increases total cost savings
- Improving the uptime/fault-free operation
Predictive maintenance is a technique that uses data analysis tools and techniques to detect anomalies in your operation and potential defects in equipment and processes. Thanks to predictive maintenance, possible failures are detected in advance and possible errors are prevented. This way, production facilities have a chance to reduce unplanned downtime as much as possible. While techniques such as oil analysis, vibration analysis, and infrared were frequently used in predictive maintenance in the past, predictive maintenance technologies have also changed and developed with the cheapening of sensors and the spread of IoT technology.
- Decrease in maintenance costs
Predictive maintenance is essential when creating a comprehensive maintenance management program for an industrial facility. While traditional maintenance programs are based on service routines for all equipment and offer rapid response to unexpected failures, predictive maintenance plans specific maintenance tasks only when they are actually needed. Therefore, one of the leading benefits of predictive maintenance is the reduction of overall maintenance costs in the business. Predictive maintenance reduces the cost of spare parts, tools and other equipment required for equipment maintenance.
- Decrease in machine breakdowns
Regular monitoring of the actual conditions of equipment and process systems significantly reduces the number of unexpected and catastrophic equipment failures. When comparing the unexpected equipment failure prior to the implementation of the predictive maintenance program and the two-year period following the inclusion of condition monitoring into the program, the failure rate drops significantly.
- Decrease in Stock Costs
The ability to predict defective parts and tools that require repair and the relevant workmanship skills reduces both repair time and costs. Industrial facilities have sufficient time to order a replacement or spare parts as needed, rather than purchasing all spare parts for stock.
- Better Production Efficiency
The availability of process systems increases after implementing a state-based predictive maintenance program. The improvement here is based on machine availability and does not include improved process returns. However, a complete predictive maintenance program that includes process parameter monitoring contributes significantly to production efficiency.